The deposition of a liquid layer onto a substrate is an essential part of the manufacturing process of coated paper for printing, adhesive tapes and labels, pharmaceutical patches, packaging materials, photoresist films for microelectronics, electrolyte and electrode sheets for advanced batteries, separation membranes, magnetic tapes and disks, coil aluminum for beverage cans and coil steel for many applications, high performance sheet glass, films for LCD displays, and many others.
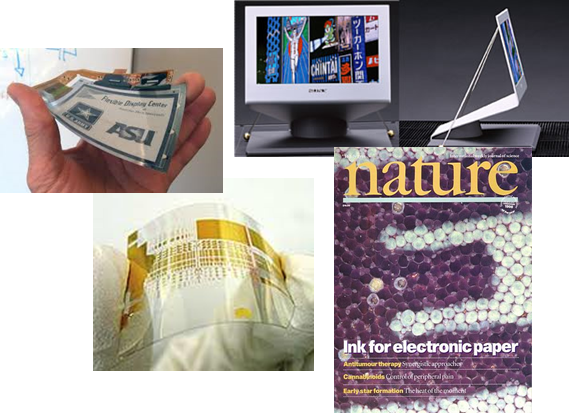
A typical coating line involves different unit operations, from mixing, liquid flow, to drying and curing. Coating is done in many different ways, leading to wide diversity of processes in different industries.
The ultimate goal of a successful coating operation is steady, uniform flow to produce a thin liquid layer of acceptable uniformity at as high a rate as possible. However, the character of the liquid flow and therefore the quality of the deposited layer depends strongly on liquid properties, the speed of coating, and other operating parameters. The search for better and less expensive products drives great technological needs for thinner coating layers for product performance or for less solvent to be dried; higher production speed; coating of more concentrated solutions and suspensions so that less solvent must be dried; shorter start-up, better control, and fewer defects, so that production yields are higher.
These needs are unlikely to be met without scientific understanding of the steps of the manufacturing process. The most critical step of a coating process is the flow in the region where the liquid is deposited on the substrate. This region is the coating bead. Its steady states and their stability to disturbances and upsets are crucial.
The research projects are focused on fundamentally understanding the process by a detailed analysis of the flow and its stability to different types of disturbances and how the liquid properties affect the process. The analysis is done both by theoretical analysis and benchtop experiments. The group at PUC-Rio has a strong long-term collaboration with the Coating Process Fundamentals Program (https://cpfp.dl.umn.edu/) at the University of Minnesota, funded by the late Prof. L.E. Scriven and directed by Prof. L. Francis, where Prof. Marcio Carvalho serves as a Graduate Faculty.
Research on these aspects is challenging. The coating bead is only a fraction of a millimeter thick and at most a few millimeters long; it is up to 2 m wide; one or both of the surfaces that confine it move at speeds up to 3 m/s and even 30 m/s in extreme cases. It is also bounded by liquid-air interfaces, i.e. free surfaces. Because of all these factors, visualization and flow measurement experiments are extremely complex. However, the investment pays off, visualizing the details of the flow in the coating bead reveals many important mechanisms that limits production.
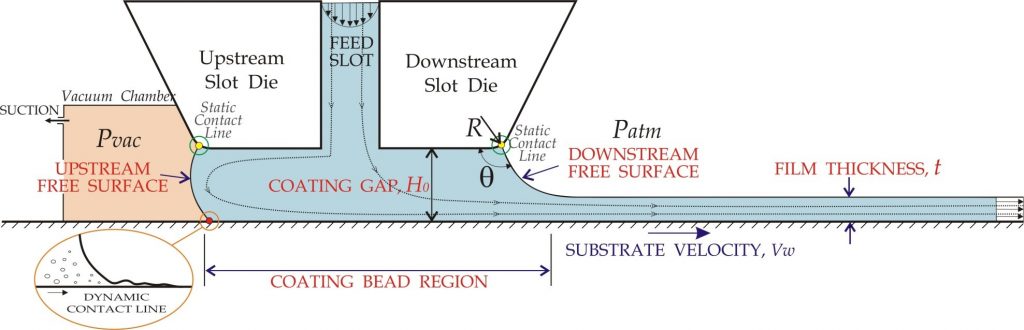
Theoretical analysis is no less challenging because it demands computer-aided solutions (usually by the Galerkin method with finite element basis functions, Newton iteration and continuation) of the governing equations, which are made nonlinear by the capillarity in free surfaces, by inertia if it is appreciable, and by non-Newtonian behavior which is often present; analysis can be further complicated by elastohydrodynamic effects of compliant confining surfaces.
Stability of steady-state solutions to three-dimensional disturbances, viscoelastic aspects of elastohydrodynamic effects, and the consequences of non-Newtonian liquid behavior are three areas least well examined, much less well understood in scientific terms.
Recent and current research projects:
Curtain coating stability
Curtain coating is widely used in the manufacturing of different products. It is a precision method that allows coating at very high speeds. However, there is a minimum film thickness that can be coated, below a critical flow rate, the curtain breaks, ruining the process.
We study the effect of liquid properties, including viscoelasticity, on the stability of liquid curtain. The results show how the wet thickness can be reduced by changing the formulation of the coating liquid, allowing coating of thin films at high speeds.
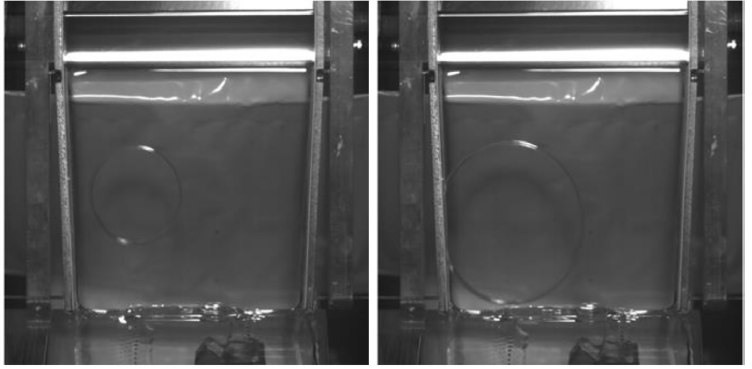
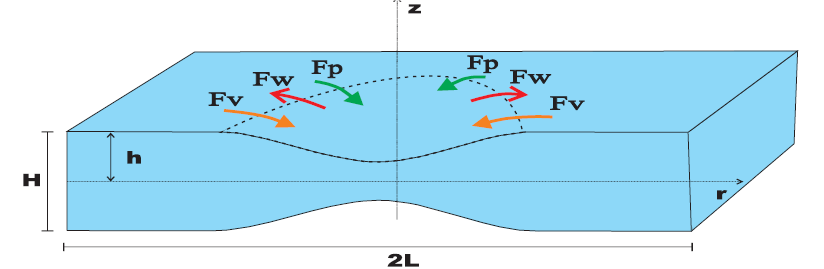
- A. M. Karim, W. J. Suszynski, S. Pujari, L. F. Francis e M. S. Carvalho, “Delaying breakup and avoiding air entrainment in curtain coating using a two-layer liquid structure”, Chemical Engineering Science, vol. 213, 115376, 2019.
- M. S. Bazzi e M. S. Carvalho, “Effect of viscoelasticity on liquid sheet rupture”, Journal of Non-Newtonian Fluid Mechanics, 264, 107–116,2019.
- A. M. Karim, W. J. Suszynski, L. F. Francis e M. S. Carvalho, “Effect of rheological properties of shear thinning liquids on curtain stability”, Journal of Non-Newtonian Fluid Mechanics, 263, 69-76,2019.
- A. M. Karim, W. J. Suszynski, W. B. Griffith, S. Pujari, L. F. Francis e M. S. Carvalho, “Effect of viscoelasticity on stability of liquid curtain”, Journal of Non-Newtonian Fluid Mechanics, Vol.257, pp. 83-94, 2018.
- A. M. Karim, W. J. Suszynski, L. F. Francis e M. S. Carvalho, “Effect of viscosity on liquid curtain stability”, AIChE Journal, Vol.64(4), 1448-1457, 2018.
Coating of particle suspension
Many coating fluids contain particles suspended in a viscous liquid, such as battery and magnetic media slurries. The functionality of the coated film is directly associated to the particle distribution in the coated film. Moreover, particle aggregation during the deposition step may lead to many coating defects, shrinking the operability window of the process.
We study the effect of shear induced particle migration and orientation in coating flows. The results show how the particle distribution and orientation in the coated film varies with process conditions. This fundamental knowledge may lead to the optimum conditions to achieve more uniform particle distribution and avoid particle aggregation in coating flows.
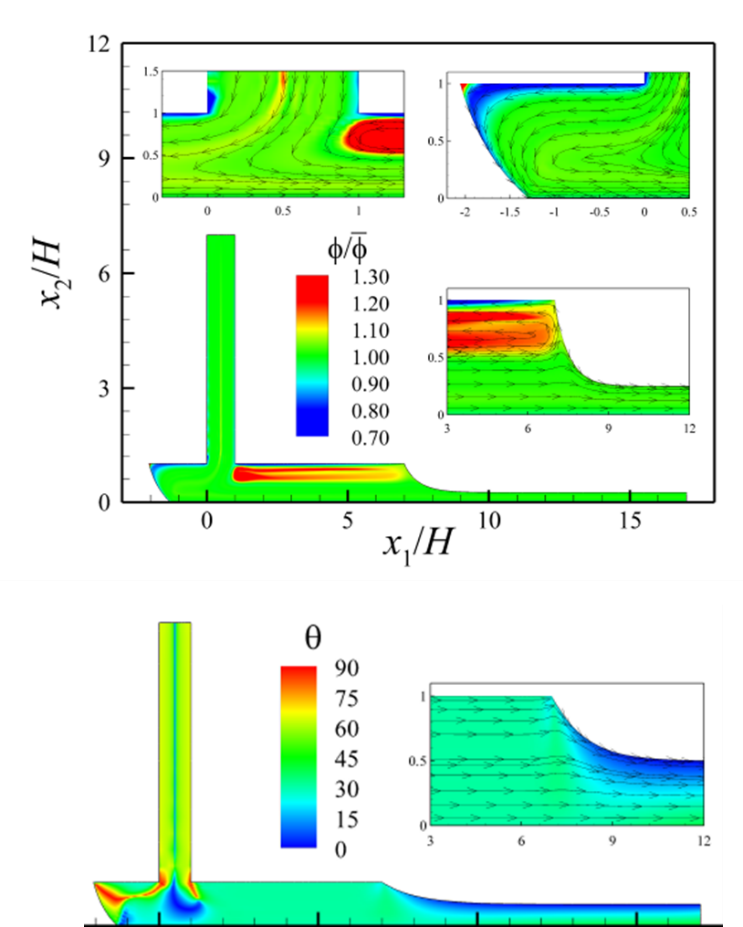
- I. R. Siqueira e M. S. Carvalho, “A computational study of the effect of particle migration on the low-flow limit in slot coating of particle suspensions”, Journal of Coating Technology and Research, vol.16(6), pp.1619-1628, 2019.
- I. R. Siqueira e M. S. Carvalho, “Shear-induced particle migration in the flow of particle suspensions through a sudden plane expansion”, Journal of the Brazilian Society of Mechanical Sciences and Engineering, vol. 40:228, 2018.
- I. R. Siqueira e M. S. Carvalho, “Particle migration in planar die-swell flows”, Journal of Fluid Mechanics, vol. 825, pp.49-68, 2017.
- S. Bochner de Araujo e M. S. Carvalho, “Sedimentation and Marangoni Stress in Slot Coating Flow of Particle Suspension”, Journal of Non-Newtonian Fluid Mechanics, vol.247, pp.53-61, 2017.
- I. R. Siqueira, R. B. Rebouças e M. S. Carvalho, “Particle migration and alignment in slot coating flows of elongated particle suspensions”, AIChE Journal, vol.63(7), pp.3187–3198, 2017.
- I. R. Siqueira, R. B. Rebouças e M. S. Carvalho, “Migration and alignment in the flow of elongated particle suspensions through a converging-diverging channel”, Journal of Non-Newtonian Fluid Mechanics, vol. 243, pp. 56–63, 2017.
- D. M. Campana, L. D. V. Silva, e M. S. Carvalho, “Slot coating flows of non-colloidal suspensions”, AIChE Journal, vol.63(3), pp. 1122–1131, 2017.
- R. B. Rebouças, I. R. Siqueira, P. R. de Souza Mendes e M. S. Carvalho, “On the pressure-driven flow of suspensions: particle migration in shear sensitive liquids”, Journal of Non-Newtonian Fluid Mechanics, vol.234, 178-187, 2016.
Liquid bridge transfer
Liquid transfer between two moving surfaces occurs in gravure printing and gravure coating. We study, in collaboration with Prof. Satish Kumar from the University of Minnesota, how different conditions affect the process and evaluate the amount of liquid that is transfer and the registration of the transferred pattern.
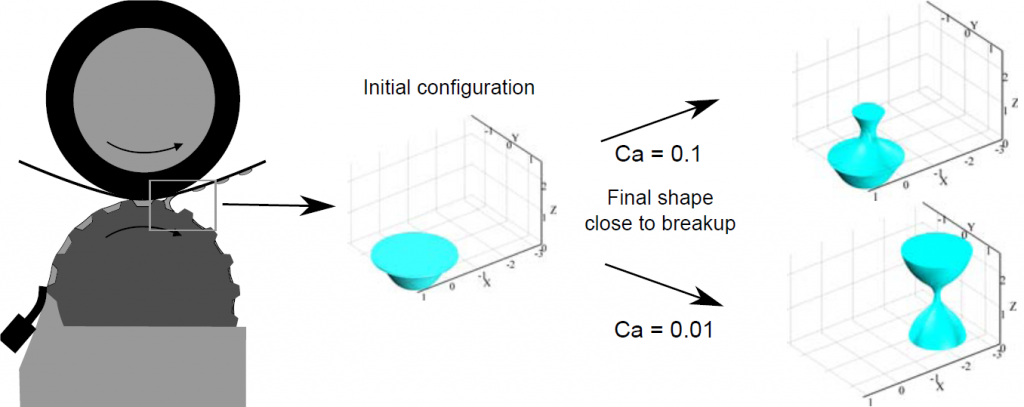
- J. T. Wu, L. F. Francis, M. S. Carvalho e S. Kumar, “Cavity Filling with Shear-thinning Liquids”, Physics Review Fluids, vol.5, 054003, 2020.
- J. T. Wu, M. S. Carvalho e S. Kumar, “Effects of Shear and Extensional Rheology on Liquid Transfer between Two Flat Surfaces”, Journal of Non Newtonian Fluid Mechanics, vol. 274, 104173, 2019.
- J. T. Wu, M. S. Carvalho e S. Kumar, “Emptying of Gravure Cavities Containing Shear-Thinning and Shear-Thickening Liquids”, Journal of Non Newtonian Fluid Mechanics, vol.268, pp.46-55, 2019.
- C.H. Huang, M. S. Carvalho e S. Kumar, “Electrostatic Assist of Liquid Transfer between Plates and Cavities”, Phys. Rev. Fluids, 4, 044005, 2019.
- J. T. Wu, M. S. Carvalho e S. Kumar, “Transfer of Rate-thinning and Rate-thickening Liquids Between Separating Plates and Cavities”, Journal of Non Newtonian Fluid Mechanics, Vol.255, pp.57-69, 2018.
- D. M. Campana, S. Ubal, M. D. Giavedoni, F. A. Saita e M. S. Carvalho, “Three dimensional flow of liquid transfer between a cavity and a moving roll”, Chemical Engineering Science, vol. 149, 169–180, 2016.
Dynamic wetting
At high speed, the wetting line of a coating process becomes unstable, leading to a three-dimensional pattern and the entrainment of small air bubbles. We study, in collaboration with Prof. Satish Kumar from the University of Minnesota, the physical phenomena that leads to air entrainment and evaluate the speed at which it occurs as a function of process conditions and liquid properties.
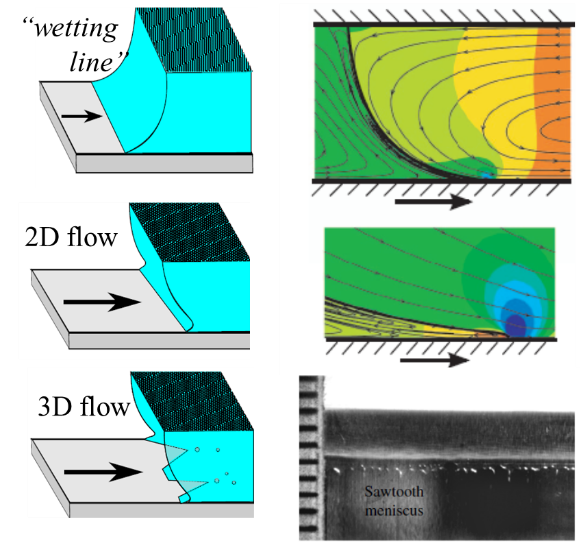
- V. Charitatos, W. J. Suszynski, M. S. Carvalho and S. Kumar, “Dynamic Wetting Failure in Shear-Thinning and Shear-Thickening Liquids”, Journal of Fluid Mechanics, 892, A1. doi:10.1017/jfm.2020.154, 2020.
- C.Y. Liu, M. S. Carvalho and S. Kumar, “Dynamic wetting failure in curtain coating: Comparison of model predictions and experimental observations”, Chemical Engineering Science, vol. 195, 74-82, 2019.
- C.Y. Liu, M. S. Carvalho and S. Kumar, “Mechanisms of dynamic wetting failure in the presence of soluble surfactants”, Journal of Fluid Mechanics, vol. 825, pp. 677-703, 2017.
- C.Y. Liu, E. Vandre, M. S. Carvalho and S. Kumar, “Dynamic Wetting Failure and Hydrodynamic Assist in Curtain Coating”, Journal of Fluid Mechanics, vol.808, 290-315, 2016.
- C.Y. Liu, E. Vandre, M. S. Carvalho and S. Kumar, “Dynamic Wetting Failure in Surfactant Solutions”, Journal of Fluid Mechanics, vol. 789, 285 – 309, 2016.